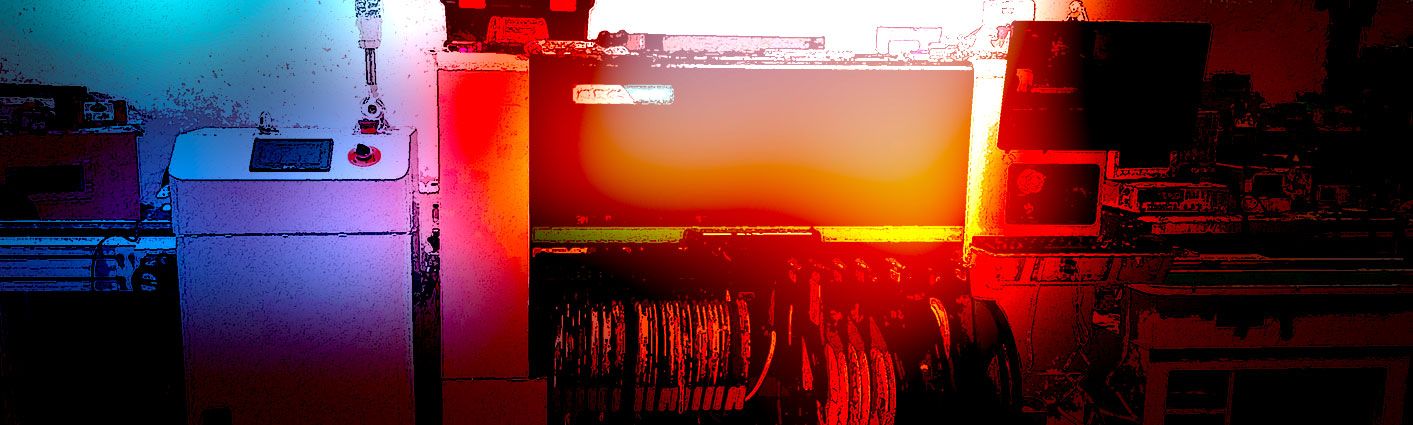
Optima’s In-House Manufacturing Is Going On-Line
Reading time: approximately 12 min
Industry Challenges
Contrary to most early predictions, the pandemic has had far reaching consequences for the entire electronics industry. Optima too has had its share of operations that were impacted. While we continue to design and manufacture quality networking devices right here in Canada, we still depend on the global electronics market. During our 23-years in business we have never seen component sourcing being impacted to such a degree. All around the globe projects have been frozen and production lines put on-hold. Manufacturers are caught in a vicious cycle of extremely constrained supplies while factory lead-times continue to rocket upwards.
Some parts have been put on allocation, others remain unobtainable for months or even years on end. Such category wide ‘bare shelves’ situations had previously been unthinkable. Many of our longest standing suppliers have been facing delays due to impaired manufacturing abilities of their own. Worldwide attempts to increase chip production have been hampered. The fact remains that the very machines needed to produce more integrated circuits cannot be made – as the required components to make more of these specialized machines, allowing the chip output to be increased, cannot be obtained.
Our Approach
Optima decided early on to purchase as many components in advance as possible. Our strategy has been to try to stock up in an attempt to smooth out the worst strains in our supply chain. Wherever feasible, we also undertook the long and arduous process of re-engineering our products. The number one aim was to enhance manufacturability in this challenging environment. Next, we focused on streamlining our internal operations. We are implementing a new ERP platform. Our goal: increase efficiency in handling everything from purchasing through manufacturing to end-customer delivery.
At the same time, we embarked on a complete transformation of our own product manufacturing. After a careful review we decided to eliminate as many of our own supply chain dependencies as we could. We invested into our own internal processes. Optima now expects its first end-to-end in-house assembly line going on-line in Q2/2022. The following paragraphs highlight a selection of events and circumstances which we encountered on our journey and the progress we made so far:
Pandemic Constrains
The pandemic delays the planning and implementation of our in-house manufacturing line. Contracted suppliers and manufacturers work under similar constraints. Some deliverables slip by months as quarantines and lock-downs take their toll on both sides of the Pacific. Undeterred, we source equipment and supplies from China, Japan, Taiwan, Korea and Hong Kong.
Lunar New Year
Despite all combined efforts, some of the production equipment we’ve ordered did not get assembled or finished in time. The traditional annual Lunar New Year holiday festival triggers factory shut-downs on a staggering scale. Our shipments are invariably put on hold until the workforce returns. After two weeks and our continued probing, work finally resumes with renewed urgency.
Overflowing Warehouses
The higher than usual pre-Lunar-New-Year rush has led to overflowing warehouses. Shipping lanes are still clogged by protracted and much delayed Q4/21 shipping volume. We learn that our orders cannot be staged for export as originally planned. Exporting warehouses are seriously overbooked. Hunting for space is incredibly frustrating and time consuming.
Switching Seaports
Our freight forwarders are frantically exploring more viable routes for each of our shipments. The decision is made to switch one of them to a different seaport, and different vessel. More delays ensue as trucks are ordered and goods make their way to the new port of exit.
Shipping Volume Headaches
More e-mail exchanges reveal that on-boarding is delayed as this unprecedented build-up of export volume is overwhelming port capacities everywhere. We anxiously await the news that our shipments have made it on-board – and more importantly, that the cargo ship is finally sailing under its own steam.
Casting Off
After some tense days, and another round of scheduling issues, we receive the news we have been waiting for: the container is stowed on-board. The container ship has cast off. The first of our cargo shipments is on its way!
Ocean Voyage
Tracking the progress of the cargo ships makes us hopeful that we will be able to receive the goods soon. What folly! After what appeared to be an excruciating wait for the container ship to cross the Pacific and arrive in North America, we later come to realize that this might have been one of the speediest legs of the whole journey.
Dead In The Water
New headaches. Backups and queued up volume at the port of entry induce further complications. The cargo ship carrying our container is forced to anchor within sight of the harbour. Everyone is being told to sit tight – and we are advised to brace ourselves for what might be weeks of waiting. It all seems to depend on how soon the ports can cope with the containers already being unloaded from earlier arrivals. Ever optimistic, we keep our fingers crossed. We hope it might not come to that and that things will get under-way again soon…
At Anchor
Days tick by. More agony. Our production staff desperately needs the goods lazily bobbing on the ocean waves, not going anywhere – while we are forced to wait. So close, yet so far!
Entry Port Still Backed Up
Finally, tracking data indicates that the cargo ship is on the move again! Hopes are quickly dashed as we realize that they are just taking up a closer anchorage position, slowly moving up to the head of the queue. As expected, more waiting ensues…
On The Quay
The ship has finally docked. Yet rail on-ramping is still delayed as the port races to complete the unloading and rail on-ramping as quickly as possible. We are getting a first-hand lesson in global supply chain logistics.Rail Strike
Disaster! No sooner do we realize that our container has finally been loaded onto a rail car that we hear that a rail strike has been called. Again, the container departure must be postponed! Our patience is being rewarded when the strike is called off after a few days and rail service resumes. Let’s call that progress.
Manitoba Blizzard
With each new day we eagerly plot the progress of the train as it traverses the Rocky Mountains, descends into the plains of Alberta, then races across the Prairies, only to hear that the weather is turning real nasty.
Environment Canada predicts up to 80cm of snowfall, claiming that the coming blizzard has not seen it’s equal in decades (which means something in a province known for its lovely winter weather). In the meantime we are glued to the weather updates on TV. Each announcer trying to outdo the other with even more dire sounding weather reports.
One Step Ahead
Environment Canada has more bleak news. The Manitoba Blizzard is moving east, pushing into Northern Ontario. Precisely where our train is heading next. However, as by some miracle, the train seems to be able to stay just one step ahead of the approaching storm front. Big shout-out to all those tireless engine crews!
Easter Holiday
More tracking reveals that the train is making its way through Ontario, finally arriving at the Inter-modal Rail Yard in Toronto on Good Friday. As everybody is off for Easter this means one thing: more waiting and delays until the Easter Weekend holiday is over… Happy Easter, everybody!
Paperwork Mix-Up
A flurry of e-mails ensues on Monday morning: there is apparently a problem with the customs paperwork. It requires immediate attention and intervention to guarantee smooth and expedited processing. Even though these days most of our communications happen electronically, it seems that problems still crop up regularly wherever the digital world meets reality.
Waiting For Clearance
More days tick by. We are itching to receive the shipment at our dock. Yet our goods have not yet been released by customs. Backlog! We call, we beg, yet we have to wait some more. So close, yet still so far.
At Last!
It’s finally here. Months later than originally anticipated, the first shipment has at last arrived. The goods have made their voyage from the other side of the globe to Toronto. Then word comes: ETA in 1 hour!
Excitement grows. We keep a sharp lookout for the delivery truck. After it docks, the real work of unloading and un-crating begins. Our team was amazing! Thanks to everyone who lent a hand. And let us not forget all those who ensured that despite it all, things got done in the end.
This is Not a Movie Script!
The foregoing tale only recounts the bumps we experienced with one of several inbound shipments. Here are some more strange or bizarre things we encountered while we desperately waited for the arrival of other goods we had ordered far in advance:Back-And-Forth
As we were running low on some supplies, we kept checking certain courier tracking updates almost hourly. We closely monitored the progress of our in-bound air freight shipment. It contained critically needed integrated circuits. Therefore, we had sprung for premium air freight. Those ICs were desperately needed to manufacture more Optima products which our customers kept ordering in unexpected quantities.All seemed to go well until the shipment hit the Cincinnati/USA hub. To our dismay, part of the shipment was routed back to Leipzig/Germany!
There, the error was discovered and the shipment was turned around. Yet rather than going back to Cincinnati, it ended up being flown to Midland/England. There it promptly got stuck. Someone over there was probably wondering the same thing we were: why was our shipment languishing in England? We worked the phones, wrote e-mails and tried our best to resolve this Gordian knot. Thankfully, the shipment finally arrived weeks late. Not the express service we had in mind or paid for!
The Wheels Came Off This One
More courier woes. As our sales continue to grow, we keep ordering larger amounts of raw materials. Shippers need to stay within maximum weight limits for each carton they ship, hence some shipments end up being distributed over multiple cardboard boxes. Nothing out of the ordinary here. We have done that for years. One such inbound air freight shipment weighed around 180kg and thus was shipped as 5 boxes. All clearly marked and labeled as belonging to a single shipment.
As ‘luck’ would have it, things got out of hand quickly. At each international hub our shipment traversed, things got split up more and more, with individual boxes being flown to different forwarding hubs in different countries. This was definitely not ‘fun’ when it came time to do customs clearance.
To top it off, we next received a carrier generated notice, informing us, that we had somehow miraculously declared that there was absolutely NO URGENCY in processing this shipment!? As a result, rather than handling it as expeditiously as possible through customs, the shipment got shunted to a different ‘express’ carrier for customs clearance. Needless to say that the individual boxes trundled in one-by-one, late, and in a sorry shape after being bounced around all over.
A Word About Quality Service
All of these quirky examples should not detract from some amazing service that our carriers still manage to deliver, no matter what the circumstances and sometimes under the most difficult of conditions. We salute those that strive to provide exemplary customer service.Without which, we at Optima could not manage to timely deliver our products to our customers. We continuously send shipments to all kinds of destinations. And we are grateful for the effort that these service providers put in to accommodate us.
A heart-felt thanks from all at Optima.

Ralf Doewich
Optima Tele.com, Inc.
Icons Credit: flaticon. Used under license.